Why Gate Valves Are an Important Component of Various Systems
- cair euromatic
- Apr 19, 2023
- 6 min read
What are Gate Valves, and How Do They Work?
Gate valves are a type of valve used to control the flow of fluids in various applications such as oil and gas pipelines, water treatment plants, and chemical processing plants. They use a gate or disc that moves up and down inside the valve body to control fluid flow. When the valve is open, the gate is lifted out of the way, allowing fluid to flow through the valve unobstructed. When the valve is closed, the gate is lowered to completely seal off the fluid flow.
Gate valves can be operated manually or automatically, with manual valves being turned by hand or wrenches. In contrast, automatic valves are controlled by an actuator driven by an electrical or pneumatic signal. One of the advantages of gate valves is their ability to provide a tight seal, which makes them ideal for applications where leak prevention is critical. Additionally, gate valves have a low-pressure drop, which does not significantly reduce the fluid flow pressure.
However, gate valves do have some limitations. They are unsuitable for applications requiring frequent opening and closing, as the gate can become damaged over time. Additionally, gate valves are not recommended for applications where the fluid is highly viscous or contains particulate matter, which can cause the gate to become stuck or clogged.
Overall, gate valves are a reliable and effective type of valve for controlling the flow of fluids in a wide range of applications, providing a tight seal and low-pressure drop. Proper maintenance and operation are important to ensure the long-term performance of gate valves in any application.
The Benefits of Using Gate Valves
Gate valves are widely used in industrial applications, including oil and gas, chemical processing, and water treatment. One of the key benefits of using gate valves is their ability to provide a tight seal, which is essential in many applications. This tight seal prevents fluid from leaking out of the valve, which can be crucial when leaks cause damage or pose a safety risk.
Another advantage of gate valves is their low-pressure drop, which does not significantly reduce the pressure of the fluid flowing through them. This is important in applications where maintaining consistent pressure is critical, such as oil and gas pipelines.
Gate valves are also durable and long-lasting, which makes them ideal for applications that require frequent use or exposure to harsh conditions. They are designed to withstand high temperatures, pressures, and corrosive substances, ensuring reliable performance.
Gate valves are easy to operate and require minimal maintenance. They can be operated manually or automatically, not requiring regular lubrication or other maintenance tasks. This reduces the overall cost of ownership and ensures that gate valves remain functional for many years.
Finally, gate valves are versatile and can be used in various applications, from simple shut-off valves to complex systems requiring precise fluid flow control. They are available in various sizes and materials to suit any application, making them a popular choice for many industries.
In summary, gate valves offer a range of benefits, including tight sealing, low-pressure drop, durability, ease of operation, and versatility. These advantages make gate valves reliable and cost-effective for controlling fluid flow in various industrial applications.
The Different Types of Gate Valves
There are several gate valves, each with a unique design and application. The most common types include the rising stem gate, non-rising stem gate, and wedge gate valves.
The rising stem gate valve features a stem that rises and lowers as the valve is opened and closed. This type of valve is commonly used in applications where it is necessary to know whether it is open or closed.
On the other hand, the non-rising stem gate valve features a stem that does not rise or lower as the valve is opened and closed. This type of valve is ideal for use in areas with limited space, as it requires less clearance than a rising stem gate valve.
The wedge gate valve is designed with a gate shaped like a wedge, providing a tight seal when the valve is closed. This type of valve is commonly used in applications requiring a tight seal, such as pipelines carrying hazardous or toxic substances.
Another type of gate valve is the slab gate valve, which features a flat gate that slides in and out of the valve body. This type of valve is commonly used in applications requiring high flow rates, such as in the oil and gas industry.
The split gate valve is another type designed with a gate that splits in half when opened. This type of valve is ideal for applications where large objects, such as rocks or debris, may become lodged.
In summary, there are several gate valves, each with a unique design and application. The choice of the valve will depend on the application's specific needs, including factors such as space requirements, flow rates, and the type of substance being transported.
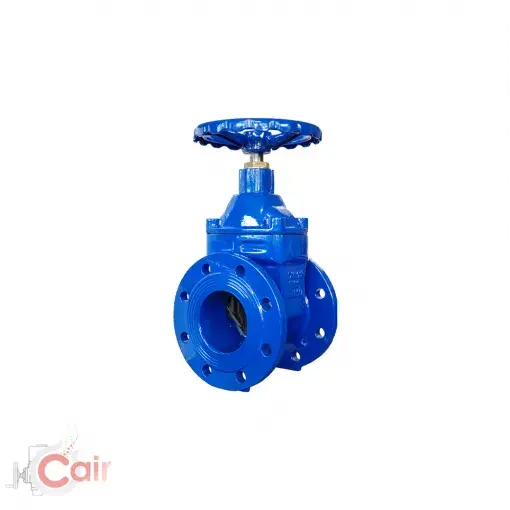
Gate Valve Maintenance
Gate valves are essential in many industrial applications, and their proper maintenance is critical to ensure their long-term performance and reliability. Regular maintenance can help prevent leaks, damage, and other issues impacting the valve's functionality. Here are some key maintenance tips for gate valves:
Inspect the valve regularly: Regular inspection can help detect any signs of wear or damage, such as corrosion, leaks, or cracks. Inspections should be done at least once a year or more frequently in high-use applications.
Lubricate the valve: Proper lubrication can help reduce friction and wear, prolonging the valve's life. To maintain valve performance, it will need to be lubricated regularly.
Clean the valve: Regular cleaning can help prevent the buildup of debris and other substances that can impact the valve's performance. Cleaning should be done using a soft-bristled brush or cloth and a mild cleaning solution.
Test the valve: Regular testing can help ensure it functions properly and detect any issues before they become more serious. This can include testing the valve's pressure and leak detection.
Replace worn or damaged parts: Over time, certain parts of the valve may become worn or damaged, and it is important to replace these parts promptly to prevent further damage to the valve.
Proper gate valve maintenance is essential to ensure its long-term performance and reliability. Regular inspection, lubrication, cleaning, testing, and replacement of worn or damaged parts can help prevent issues and prolong the valve's life. It is important to follow the manufacturer's recommended maintenance procedures and seek professional assistance if needed.
Why Gate Valves are an Important Component of Various Systems
Gate valves are essential to many industrial systems, including oil and gas pipelines, chemical processing plants, water treatment facilities, etc. Here are some reasons why gate valves are an important component of these systems:
Control fluid flow: Gate valves are designed to control the flow of fluids, such as liquids or gasses, through a pipeline or system. They can completely shut off or adjust the flow rate as needed.
Provide a tight seal: Gate valves are designed to provide a tight seal when closed, which is essential in applications where leaks can pose a safety hazard or cause damage to equipment or the environment.
Low-pressure drop: Gate valves have a low-pressure drop, which means they do not significantly reduce the pressure of the fluid flowing through them. This is important in applications where maintaining consistent pressure is critical, such as oil and gas pipelines.
Durability: Gate valves are designed to withstand high temperatures, pressures, and corrosive substances, ensuring reliable performance over time. This makes them ideal for applications that require frequent use or exposure to harsh conditions.
Easy to operate: Gate valves can be operated manually or automatically and do not require regular lubrication or other maintenance tasks. This reduces the overall cost of ownership and ensures that gate valves remain functional for many years.
Versatility: Gate valves are available in various sizes and materials to suit any application, making them a popular choice for many industries. They can be used in various applications, from simple shut-off valves to complex systems requiring precise control over the fluid flow.
In summary, gate valves are important to various systems because they control fluid flow, provide a tight seal, have a low-pressure drop, and are durable, easy to operate, and versatile. Their ability to reliably control fluid flow in various applications makes them essential in many industrial systems.
Cair Euromatic Automation is the leading gate valve manufacturer in India. We offer various industrial valves, like ball valves, butterfly valves, control valves, and many more.
コメント