Advantages of Non Slam Check Valves in Fluid Control Systems
- cair euromatic
- Aug 16, 2023
- 5 min read
Water hammer, a hydraulic shock caused by sudden changes in fluid velocity, can wreak havoc on fluid control systems. A non slam check valve emerges as crucial solutions in preventing water hammer and its associated risks. These valves play a pivotal role in managing fluid flow dynamics and ensuring the integrity of the entire system. Here's how they effectively mitigate water hammer:
Slow Closure: Unlike traditional check valves that close abruptly, non slam check valves employ a controlled closing mechanism. This gradual closure significantly reduces the abrupt stop of fluid flow, curbing the development of pressure spikes.
Flow Reversal Management: When flow direction changes suddenly, water hammering can occur. Non slam check valves are engineered to handle this transition smoothly, preventing the sudden impact that contributes to hydraulic shock.
Minimized Pressure Surges: By avoiding the rapid acceleration or deceleration of fluid, non slam check valves help maintain stable pressure levels throughout the system. This mitigates the likelihood of pressure surges that lead to water hammer.
Reduced Noise: The controlled closure of non slam check valves results in significantly quieter operations compared to their traditional counterparts. This noise reduction is an additional benefit stemming from their ability to prevent water hammering.
Incorporating non slam check valves in fluid control systems presents a proactive approach to preventing water hammering. These valves not only safeguard equipment and pipelines from damage but also enhance overall system longevity. By mitigating the risks associated with water hammer, non slam check valves ensure smoother operations, reduced maintenance needs, and enhanced safety – all contributing to the optimized performance of fluid control systems.
Enhanced System Integrity: Maintaining Pipe and Component Longevity
In fluid control systems, the integration of non-slam check valves brings forth a range of advantages that contribute to the overall integrity and longevity of pipes and system components. These benefits are pivotal in ensuring smooth and efficient operations while minimizing the risks of damage and costly repairs. Here's how non-slam check valves play a crucial role in enhancing system integrity:
Elimination of Hydraulic Shock: Non-slam check valves prevent the abrupt reversal of fluid flow, which can result in a destructive water hammer. This safeguard effectively shields pipes and associated components from the detrimental impacts of sudden pressure surges.
Reduction of Stress and Fatigue: The gentle closure mechanism of non-slam check valves significantly reduces stress and fatigue on pipes and fittings. This prolonged avoidance of rapid pressure changes helps extend the service life of these vital components.
Minimized Erosion and Corrosion: By ensuring a controlled and steady flow direction, non-slam check valves mitigate the erosion and corrosion that can be triggered by turbulence and sudden flow changes.
Consistency in Operations: The consistent and controlled flow facilitated by non-slam check valves prevents the wear and tear that can arise from irregular fluid movement.
Cost-Effective Maintenance: With reduced wear and stress on pipes and components, maintenance requirements are lowered, translating to decrease operational costs over time.
Incorporating non-slam check valves into fluid control systems is not only an investment in operational efficiency but also a proactive step toward maintaining the longevity and integrity of pipes and components. These valves effectively protect the infrastructure, ensuring sustained functionality and minimizing the risk of unexpected failures.
Noise Reduction: Quieting Operations with Non Slam Check Valves
In fluid control systems, the noise generated by hydraulic shock and sudden pressure changes can be a considerable concern. Non Slam Check Valves offer an effective solution to mitigate this issue, making them an essential component in noise-sensitive environments. Here's how these valves contribute to noise reduction:
Hydraulic Shock Suppression: Non slam check valves are specifically designed to close gradually, preventing the abrupt closure that causes hydraulic shock, which in turn generates noise.
Smooth Flow Transition: These valves ensure a controlled flow reversal by allowing the fluid to change direction gradually, minimizing turbulence and noise associated with rapid pressure changes.
Elimination of Water Hammer: By preventing water hammer, non slam check valves help avoid the sharp pressure spikes that produce loud banging sounds in piping systems.
Operational Quietness: The gradual closing and opening mechanism of non slam check valves significantly reduces the noise generated during regular valve cycles.
Incorporating non slam check valves into fluid control systems not only enhances operational efficiency but also creates a quieter and more comfortable working environment. Whether in industrial settings or residential applications, the noise reduction benefits of non slam check valves contribute to overall system harmony and functionality.
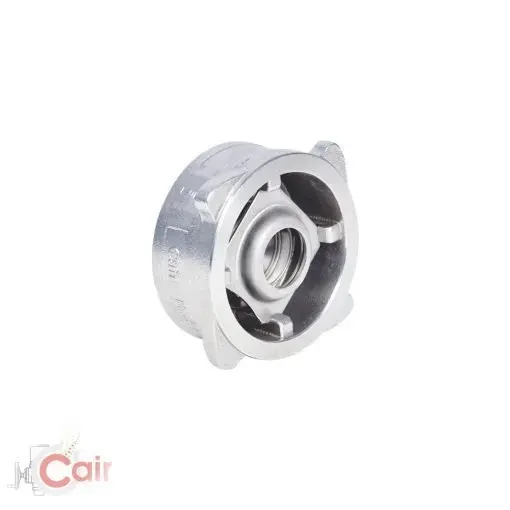
Improved Energy Efficiency: Optimizing Fluid Flow and Pump Performance
In fluid control systems, the integration of non-slam check valves introduces a host of advantages that contribute to heightened energy efficiency. These valves, specifically designed to mitigate the negative impacts of water hammer and reverse flow, play a pivotal role in streamlining fluid movement and enhancing pump performance.
Smooth Flow Regulation: By promoting consistent fluid flow, non-slam check valves eliminate turbulent surges that can strain pumps and pipelines. This steadier flow ensures that pumps operate optimally, requiring less energy to maintain desired flow rates.
Reduced Pump Wear: The elimination of slamming effects and reverse flow minimizes wear and tear on pumps, allowing them to operate within their designed parameters. This reduced strain translates to extended pump life and decreased energy consumption.
Enhanced System Stability: With the prevention of water hammer, the overall system remains more stable, reducing the need for corrective actions that can disrupt the energy efficiency of the entire operation.
Incorporating non-slam check valves into fluid control systems not only safeguards against pressure-related inefficiencies but also optimizes pump performance. The resultant reduction in energy consumption aligns with sustainable practices and cost savings while ensuring the consistent and efficient operation of industrial processes.
Reduced Maintenance: Long-Term Reliability and Lower Downtime
Non slam check valves play a pivotal role in fluid control systems by significantly reducing maintenance requirements, thereby enhancing long-term reliability and minimizing downtime. Here's how they achieve this:
Minimized Wear and Tear: Non slam check valves' unique design prevents sudden closure, mitigating the stress on system components and reducing wear, which in turn extends their operational life.
Lessons Erosion: The absence of slamming action reduces the erosive forces that could damage valve internals and adjoining pipelines, ensuring sustained performance over time.
Lower Fouling: With the elimination of the water hammer, the risk of particulate buildup and debris accumulation in the system decreases, resulting in smoother operation and fewer blockages.
Diminished Valve Failures: By preventing water hammer-induced pressure spikes, non slam check valves contribute to fewer valve failures, minimizing the need for unscheduled maintenance or replacement.
These advantages cumulatively lead to a fluid control system that is not only reliable over the long term but also experiences reduced downtime due to maintenance, making non slam check valves a valuable asset in maintaining operational efficiency and productivity.
Backflow Prevention: Safeguarding Upstream Equipment and Processes
Backflow, the undesirable reversal of fluid flow in a piping system, poses significant risks to both equipment and processes in fluid control systems. Non slam check valves play a vital role in mitigating these risks by preventing backflow and maintaining the integrity of the entire system. Here's how they achieve this:
Unidirectional Flow Control: Non slam check valves ensure fluid movement in only one direction, eliminating the possibility of backflow that could damage or contaminate upstream equipment.
Maintaining Process Efficiency: By preventing backflow-induced disruptions, non slam check valves enable consistent flow rates and pressure levels, contributing to optimal process efficiency.
Protecting Sensitive Components: Upstream equipment, such as pumps and meters, are shielded from the damaging effects of backflow, extending their operational lifespan.
Contaminant Prevention: Non slam check valves block the ingress of unwanted substances that could compromise the quality of fluids and end products.
Compliance Assurance: Industries with strict regulatory requirements, such as water treatment and food processing, can rely on non slam check valves to adhere to safety and quality standards.
Incorporating non slam check valves into fluid control systems ensures reliable backflow prevention, safeguarding equipment functionality, process effectiveness, and regulatory compliance.
Comentarios